Our industry-leading, high-speed industrial robots include high-payload, extended-reach, ultra-maneuverable seven-axis and unique 15-axis dual-arm robots.
Automated laboratory tests with robots
Robots have long-since become established in industry, and automation is also gaining a foothold in laboratory environments. In research and development (pharmaceutical, chemistry, life science, bio- and nuclear medicine), blood analysis and individual cosmetics production, convincing results have been achieved over many years with robot solutions that are so flexible and versatile that they are also suitable for clinical infection tests. Besides easing the burden on laboratory staff, robots offer excellent and reliable process stability and quality.
There are basically two forms of robot-supported automation of lab processes:
a) Partial automation, in which the robot performs the repetitive actions of the laboratory staff, thus facilitating routines. The robot assumes handling tasks, but process control remains with lab personnel or automatic analysis systems.
b) Full automation of the testing procedure, including sample preparation, pipetting, test implementation and operation of all analytical equipment by the robot. The robot assumes process control and handling tasks. The aim is to construct universally usable standard work cells, with a two-arm robot as a central element that can be adapted and flexibly reprogrammed to any lab equipment. A solution of this kind can independently carry out lab processes 24 hours per day with the highest precision and repeatability.
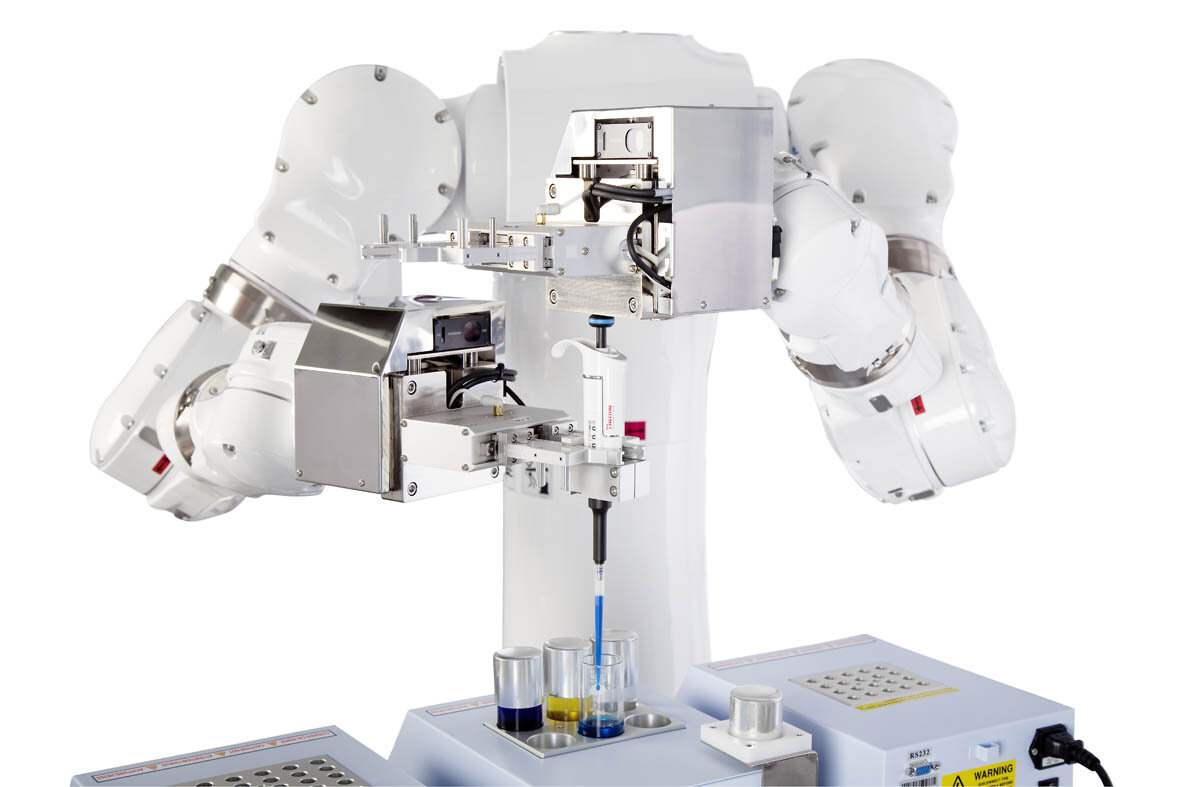
How fast can robot-supported automation solutions be installed?
Partial automation, i.e. retrofitting a robot for handling purposes, can be quickly completed with collaborative robots. In comparison, the design and installation of a new, fully automated robot cell takes several months. But once a standard robot cell of this kind has been constructed, the laboratory and analytical equipment has been installed around the robot with a gradually growing library of motion patterns, “these cells can be quickly and simply reprogrammed for new tasks,” says Thomas Goldfuss, General Manager of Goldfuss Engineering Company that has already implemented several laboratory cells with Yaskawa robots for renowned customers.
Fast solution: partial automation of handling tasks with a collaborative robot
Short-term relief of the laboratory staff can be achieved by partial automation of handling tasks at existing manual test stations. The robot performs repetitive movements, thus lifting the burden on qualified lab personnel. A collaborative robot that can be used in direct contact with humans and does not require a safety guard is predestined for the purpose.
One such robot is Yaskawa’s MRK-capable MOTOMAN HC10DT. Two versions of the six-axis robot are particularly suitable for use in the laboratory. These are the dust- and waterproof HC10DT IP67 (designed to meet the protective requirements of protection class IP67) and the hygienically designed HC10DTF, whose operating materials and gear grease are approved for contact with foodstuffs.
With the Direct Teach (DT) process the robot arm is simply guided from point-to-point in a sequence of motions. With the aid of pre-assigned pushbuttons on the robot, the operator can specify whether a gripper is to be opened or closed at certain positions. This motion sequence is saved in a library, and the robot can repeat it any number of times. To do this, the operator does not need to be a robot programming expert.
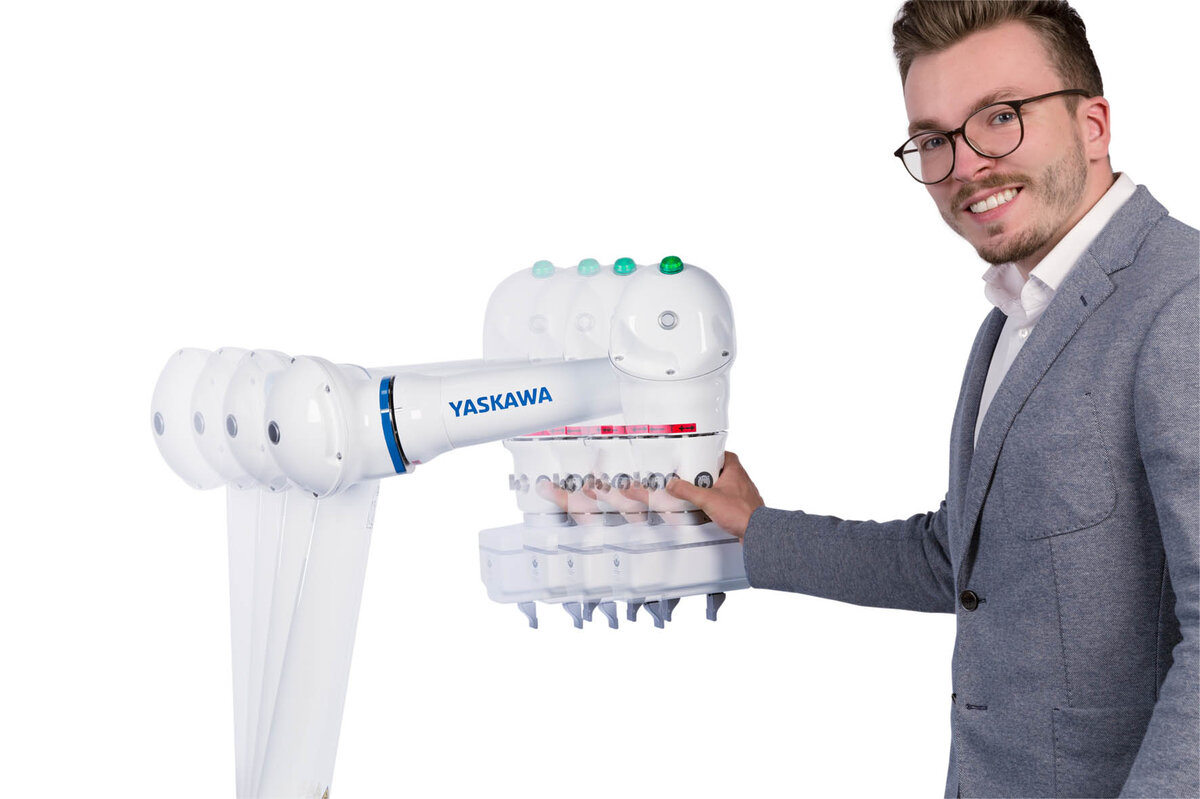
Fully automatic workstation – with the CSDA10F two-arm lab robot
A robot specially developed for lab automation is Yaskawa’s two-arm MOTOMAN CSDA10F robot. With its human-like stature and two arms capable of individual or synchronized movements, thanks to multifunctional tools and grippers it is extremely versatile in use. It can work with almost any existing standard lab equipment and is able to handle conventional laboratory equipment as known from manual workstations: e.g. petri dishes, manual pipetting, incubators or reaction vessels. Automation-friendly equipment such as pipettors with expensive tips or microtiter plate stations are helpful in respect of accelerating throughput, but unnecessary.
The existing analytical equipment is adopted in its present form including software connections, even though it was not actually optimized for classical automation. Expensive liquid handling systems – with their costly consumable materials – are not strictly necessary, as the robot can directly assume this task. In its laboratory workstation the robot can perform a wide range of tasks that had hitherto been reserved for humans, such as the opening and closing of reaction vessels (not necessarily microtiter plates), pipetting and dosing of liquids or powders, production of nutrient solutions with spatulas. Furthermore, they can be used for the insertion and removal of samples as well as opening, filling and closing of reaction vessels, or the operation of devices such as centrifuges, vibrators or incubators.
The CSDA10F is ideally suited to complex, standardized test sequences according to protocols that were written for manual operation. The two-arm CSDA10F robot is also an interesting solution in process development, e.g. for the definition, safeguarding and optimization of process stages prior to the upscaling of throughput in a later production line. In Japan it is already being employed in larger installations for biomedicine synthesis (cancer drug development) and chemical analysis (sample preparation).
The CSDA10F is based on a robot that has already had a major impact on industry automation. This new version was specially designed to satisfy hygiene requirements in the laboratory, e.g. with a highly substance-resistant finish, washable hygienic design, H2O2 sterilization and cleanroom compatibility acc. to ISO 14644-1.
Due to its high degree of flexibility, the range of applications for the innovative robot is broadly diversified – it can quickly and easily learn completely new work processes. Many characteristic movements (pipetting, opening/closing of “eppis”, handling microtiter plates, opening/closing of incubators or screw-top bottles) were already standardized and appropriately stored as modules in a movement library. The interface human/robot for operation and visualization can be realized via a PC or a touch panel. The HMI is either individualized or connected to an existing workflow scheduling software (e.g. SAMI-EX from Beckman Coulter). Once the movement programs are stored in the library, the robot operator does not need to be an expert; the latter simply composes and parameterizes the individual process stages of the desired work sequence.
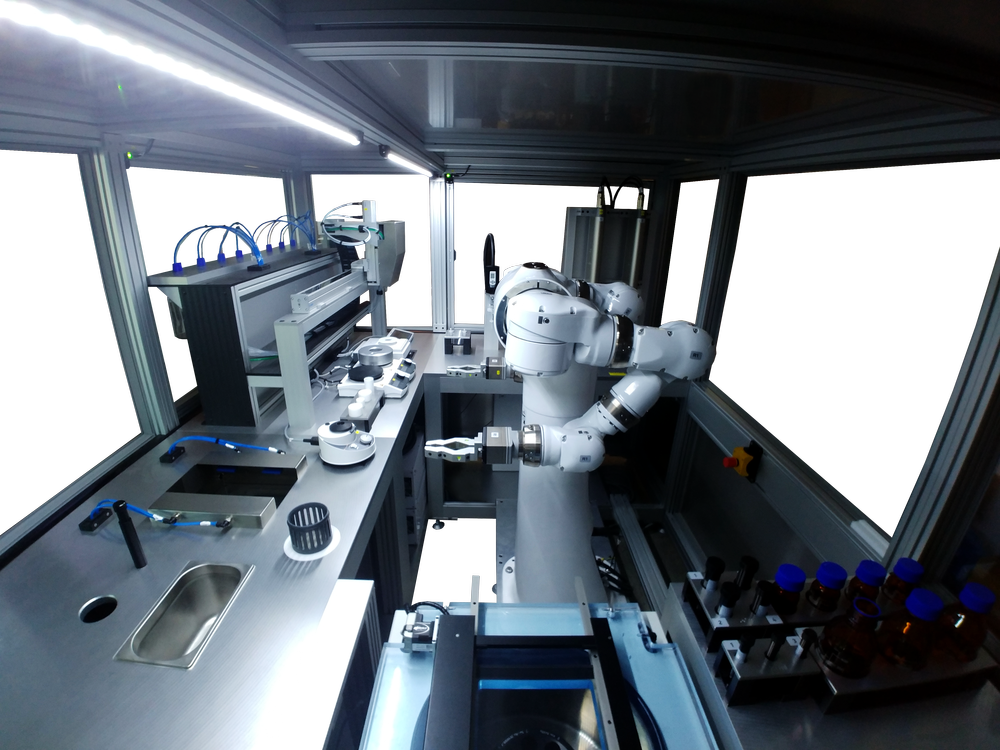
Summary
Until now, classical automation in laboratories was often deemed to be inflexible and bulky. Today, easy-to-operate robot models are available that can carry out a multitude of different laboratory tasks. They can perform operations that are too dangerous or monotonous for humans. The use of robots also guarantees exact reproducibility of work results in the processing of many samples. Lab automation not only saves time and costs, particularly with high throughput rates. Due to the unrivalled level of precision, it creates new prerequisites for research on input materials, the production of which was hitherto not sufficiently reliable or reproducible.
Author and contact:
Christopher Schneider,
Product Manager Collaborative Robots
Yaskawa Europe GmbH – Robotics Division
Yaskawastr. 1 – 85391 Allershausen
Tel. +49-8166-90-0
robotics@yaskawa.eu.com