Our industry-leading, high-speed industrial robots include high-payload, extended-reach, ultra-maneuverable seven-axis and unique 15-axis dual-arm robots.
Handover of a Yaskawa HC10 cobot to the Reconfigurable Robotics Lab at EPFL
A robot for robotics research
The Reconfigurable Robotics Lab (RRL) at EPFL conducts research into the development of innovative robotic systems such as soft and origami robots – now with the support of a Yaskawa Cobot HC10. The robot was officially handed over on 28 May.
Consisting of triangular or polygonal modules, they can be assembled to create a wide variety of shapes and are able to move in all directions. “Our robots are inspired by the Japanese art of paper folding. That’s why we call them ‘reconfigurable origami robots’,” explains Alexander Schüßler, doctoral student at the Reconfigurable Robotics Lab (RRL), a research unit at the Swiss Federal Institute of Technology in Lausanne (EPFL).
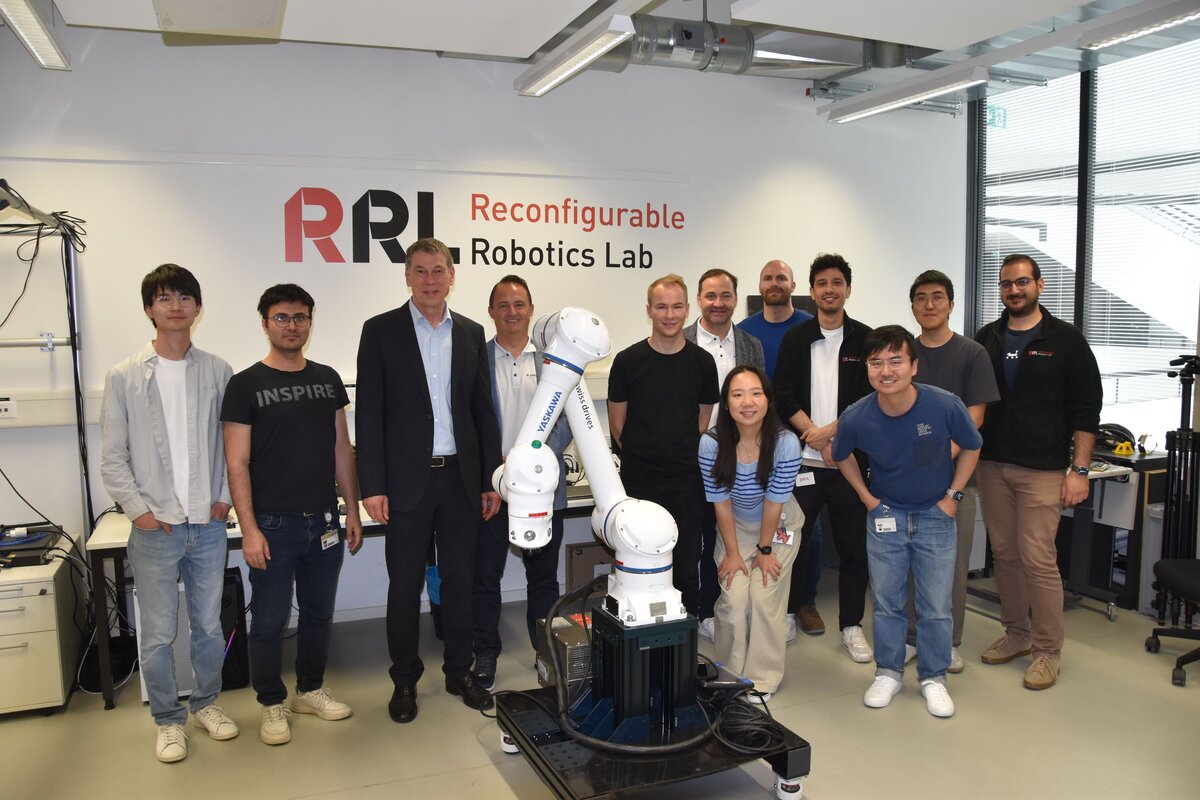
Image: Representatives of Yaskawa Europe GmbH and SwissDrives AG at the handover of the cobot to the Reconfigurable Robotics Lab (RRL) at the Swiss Federal Institute of Technology in Lausanne (EPFL).
Research at the lab is dedicated to inventing interactive robotic systems with novel manufacturing techniques and integration processes that push the boundaries of mechanical properties. These efforts enable the development of soft, reconfigurable and interactive robots that are highly aware of the environment, so they are expected to have extensive applications in wearable technology, medical/rehabilitation systems and personal robots.
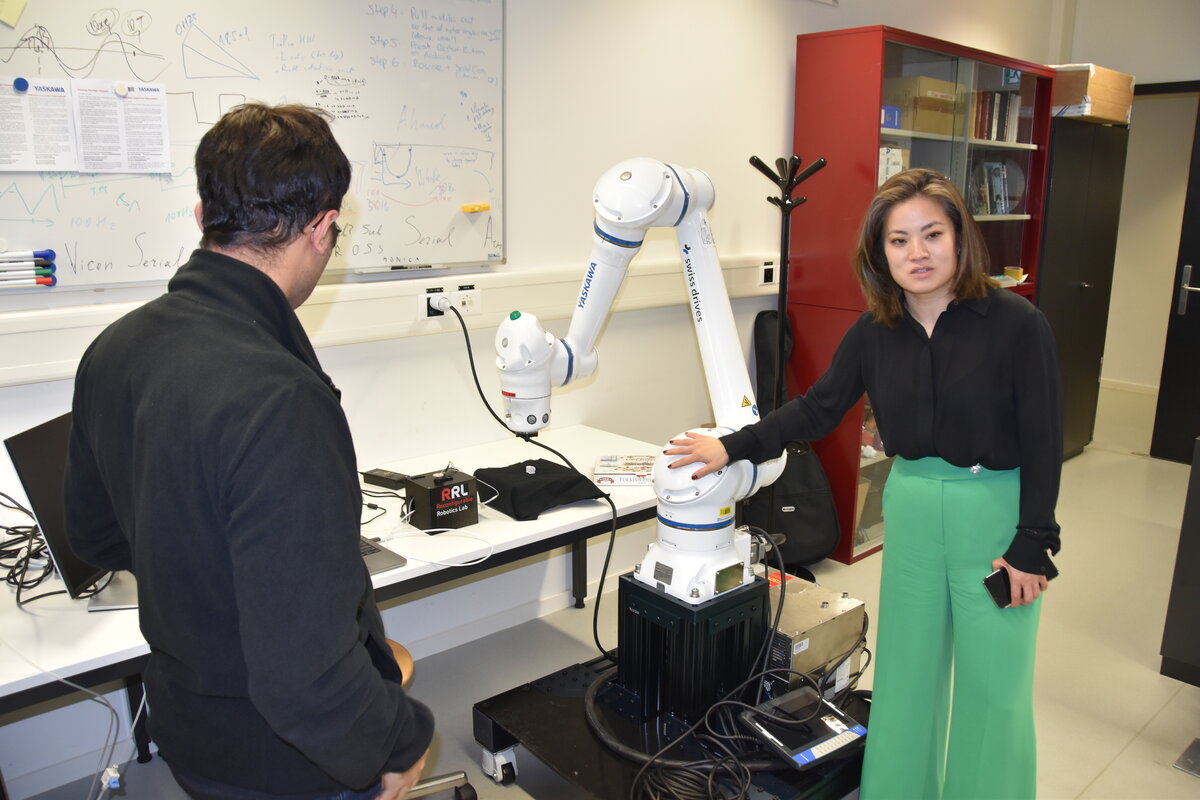
Image: Professor Jamie Paik explains the use of the HC10 in tactile sensor research.
Cobot or robot – depending on requirements
The RRL at EPFL was established 12 years ago, and the team there is made up of scientists from diverse disciplines. They have access to a wide range of tools and equipment for their research, but the lab did not previously make use of industrial robots. “That might sounds a bit unusual for a robotics lab,” says Alexander Schüßler.
High-precision, top-quality work were key criteria in the selection process: use of the new “research assistant” in experiments makes the results repeatable and reproducible, so the is data more reliable.
A Yaskawa Cobot HC10 has been supporting the team in its research since 28 May 2024. The 6-axis robot with a payload capacity of 10 kg and an absolute working range of 1,379 mm (effective range 1,200 mm) is a cobot – a collaborative robot – so it is suitable for fenceless operation, enabling straightforward and secure collaboration between humans and robots. Depending on requirements, the HC10 can also be deployed as a high-quality industrial robot, securely monitored and capable of operating at full power and speed.
Impressive precision and speed
“The industrial robot offers impressive precision,” says Alexander Schüßler. “We’re researchers so we’re used to our robots posing all kinds of challenges – it’s normal for us to be busy solving problems and getting to grips with faults and malfunctions. The HC10 is completely different: even the installation was very straightforward. Now we can simply switch it on and it carries out all movements to the very highest standards in terms of precision and quality.”
At the moment the HC10 is primarily deployed to carry out force measurements and collect data on the behaviour of the reconfigurable robots when they make fast movements. “Precision and speed were crucial requirements for us, and only Yaskawa was able to offer this. What is more, Yaskawa’s Swiss partner SwissDrives AG provided us with excellent advisory services and technical support,” says Alexander Schüßler.
Combined with its comprehensive application expertise, Yaskawa’s portfolio offers every customer real added value, so SwissDrives is very keen to expand its market share throughout Switzerland on a lasting basis.
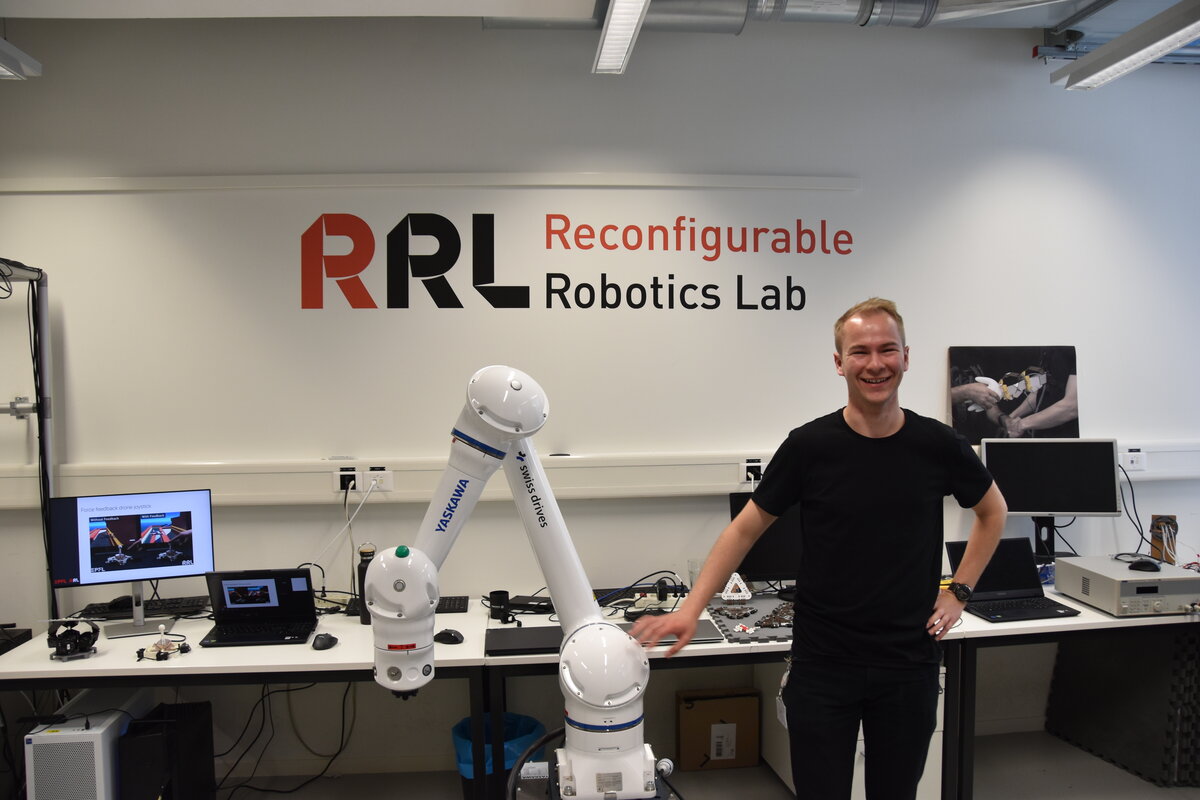
Image: Alexander Schüßler, doctoral student at EPFL.
ROS 2 as a common platform for cobots, reconfigurable robots and sensors
The researchers connect the cobot controller and the controller of the reconfigurable robots via the Robot Operating System ROS 2, a flexible and modular open-source software platform supported by Yaskawa. Other sensors can also be connected to ROS 2 – for pressure and infrared, for example. “We can collect data on human-robot interactions for instance, even if they’re not in the same place. That’s known as ‘remote human interaction’,” explains Schüßler.
RRL Associate Professor Jamie Paik is delighted with her new assistant, too: the HC10 not only enables the researchers to obtain much more data in their experiments, the data is also more accurate. “Reproducibility, repetition and consistency are absolutely vital in scientific research,” says Jamie Paik. Venturing a look ahead, Paik adds: “Today the cobot enables us to conduct new types of experiments, but in the future it may also open up new possibilities and fields of experimentation that we’re not even aware of right now.”
Managing Director of Yaskawa Europe GmbH Bruno Schnekenburger says: “For years now, supporting educational and research institutions has been a matter of course for us. Yaskawa’s mission is to make people’s lives easier and use its technology to make a contribution for the future. This is why Yaskawa also supports the ROS2 interface, which is primarily used in the university and research environment.
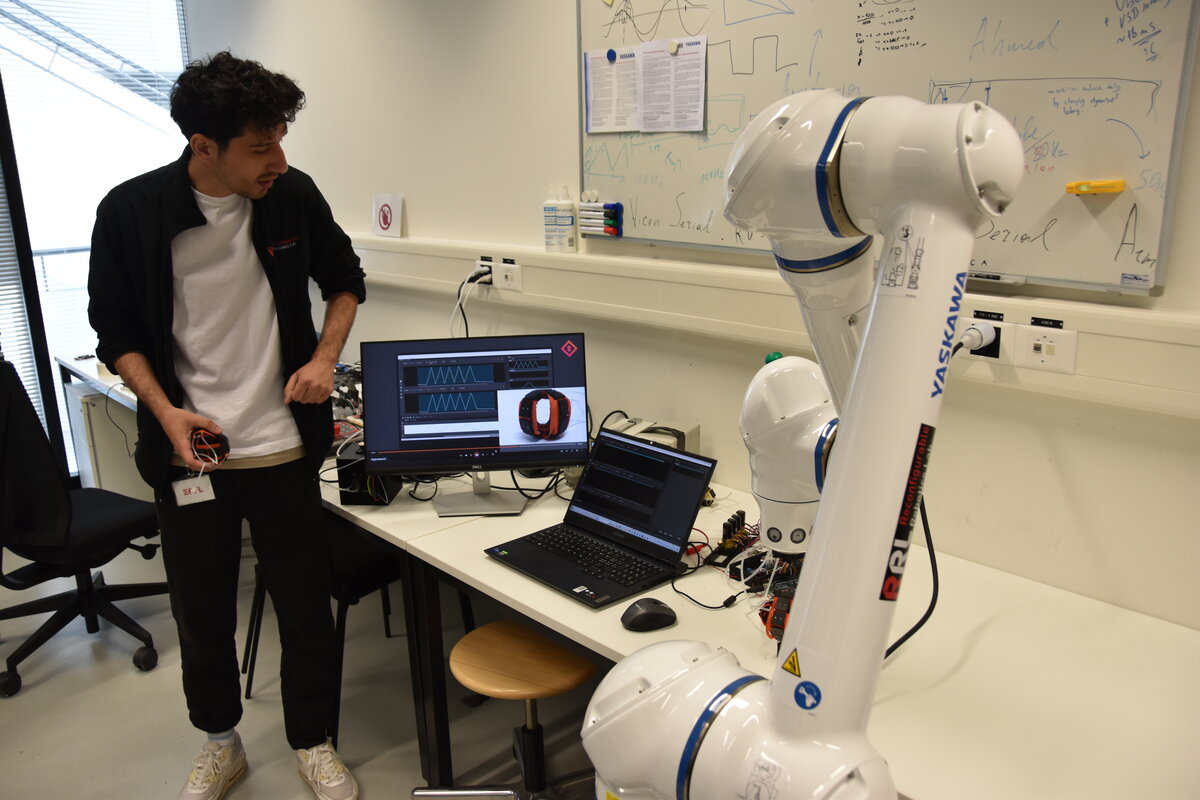
Image: The cobot supports the measurement of a “robot squeeze ball”.
The Reconfigurable Robotics Lab(RRL) at the Swiss Federal Institute of Technology in Lausanne (EPFL).
The RRL conducts research into the design, drive technology, manufacture and control of interactive robotic systems that overcome the limitations of traditional robotic systems. These include innovative robot concepts such as origami robots and soft robots, new technologies for drive and sensor systems, and also modelling and control.
With around 12,000 students and doctoral students from over 120 countries and more than 370 laboratories, the Swiss Federal Institute of Technology in Lausanne (École Polytechnique Fédérale de Lausanne, EPFL) is one of Switzerland’s leading technical and scientific universities. It is actively involved in areas such as renewable energies, medical technology, neurotechnologies, material sciences and information technologies.
Source for all images: Yaskawa Europe GmbH
Contact for readers’ enquiries:
Phone +49-8166-90-0
robotics@yaskawa.eu
www.yaskawa.de
Contact for the press:
Yaskawa Europe GmbH
Richard Tontsch
Philipp-Reis-Straße 6
D-65795 Hattersheim, Germany
Tel. +49 (0) 171-5523816
E-Mail: richard.tontsch@yaskawa.eu
www.yaskawa.de