Our industry-leading, high-speed industrial robots include high-payload, extended-reach, ultra-maneuverable seven-axis and unique 15-axis dual-arm robots.
Masks “made in Germany”
Flexible automation technology for special purpose machinery manufacture
With the arrival of the coronavirus pandemic, the need for FFP2 respirator masks increased exponentially. In the early days, however, there was a lack of production capacity. That changed quickly in the course of 2020. Experienced mechanical engineers reacted promptly and were able to offer efficient solutions “made in Germany” within an astonishingly short time. One provider who very quickly implemented a machine concept in collaboration with automation specialist Yaskawa is special machine manufacturer Unimatic Automationssysteme GmbH from Grub am Forst near Coburg. The concept was the result of powerful drive and control technology from Yaskawa combined with good teamwork between the two partners.
When the government discovered in March 2020 that there was a shortage of medical protective equipment, it commissioned German companies to manufacture it. However, most of them did not have the appropriate facilities. This is how Unimatic Automationssysteme GmbH came to receive an inquiry from a customer about the possibility of constructing a production system for FFP2 respirator masks within a short period of time. The special machine manufacturer did not hesitate to accept the challenge. The firm called in colleagues from Unimatic China, who already had valuable experience in this field. “In a joint venture with China, we developed the system concept and adapted it to the standards of the European market,” reports Dr. Robert Kahlau, head of the Robotics department at Unimatic. “The customer initially ordered four systems, but the final order was for a total of eight production lines.”
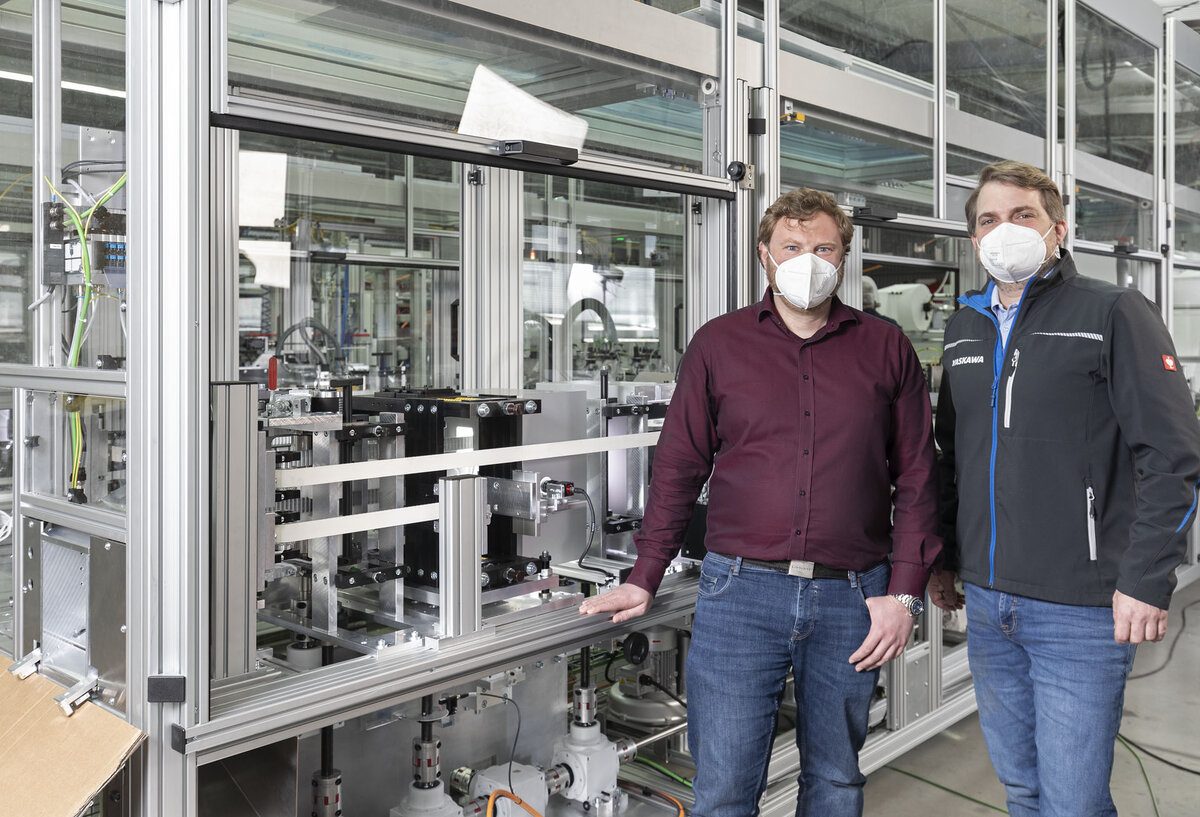
Fully automatic assembly system for FFP2 protective masks
The assembly systems are designed for the fully automatic production of FFP2 or KN95 masks with straps for fastening around the head. With a length of 10 m, a width of 1.5 m and a height of 2 m, the systems are very compact and can produce 40 masks per minute. The machine output of the masks is limited by the long elastic straps. The multi-layer material from which the masks are made is also not easy to process. The material is therefore transported through the system at a constant speed. The ultrasonic welding systems function as flying saws. The special material properties place particular demands on this manufacturing process, which requires high-performance, precisely synchronized drive technology.
Bringing the system to market within a few months was an outstanding achievement. The schedule was tight and the machine manufacturer also had to process the order alongside its daily operations. Speed, flexibility and programming capabilities also presented serious challenges. “When producing the masks, we had to deal with three complex technical issues: the flying saw, the ultrasonic processing of the embossing contour and the cutting technology,” remembers Dr. Kahlau. “In order to arrive at an efficient solution quickly and safely, we recruited competent partners who provided us with the necessary knowledge. We relied heavily on flexibility, particularly where quick decisions were needed, and on the willingness of the entire team to cooperate—both with each other and with our partners—in order to complete the project within the shortest possible time frame.”
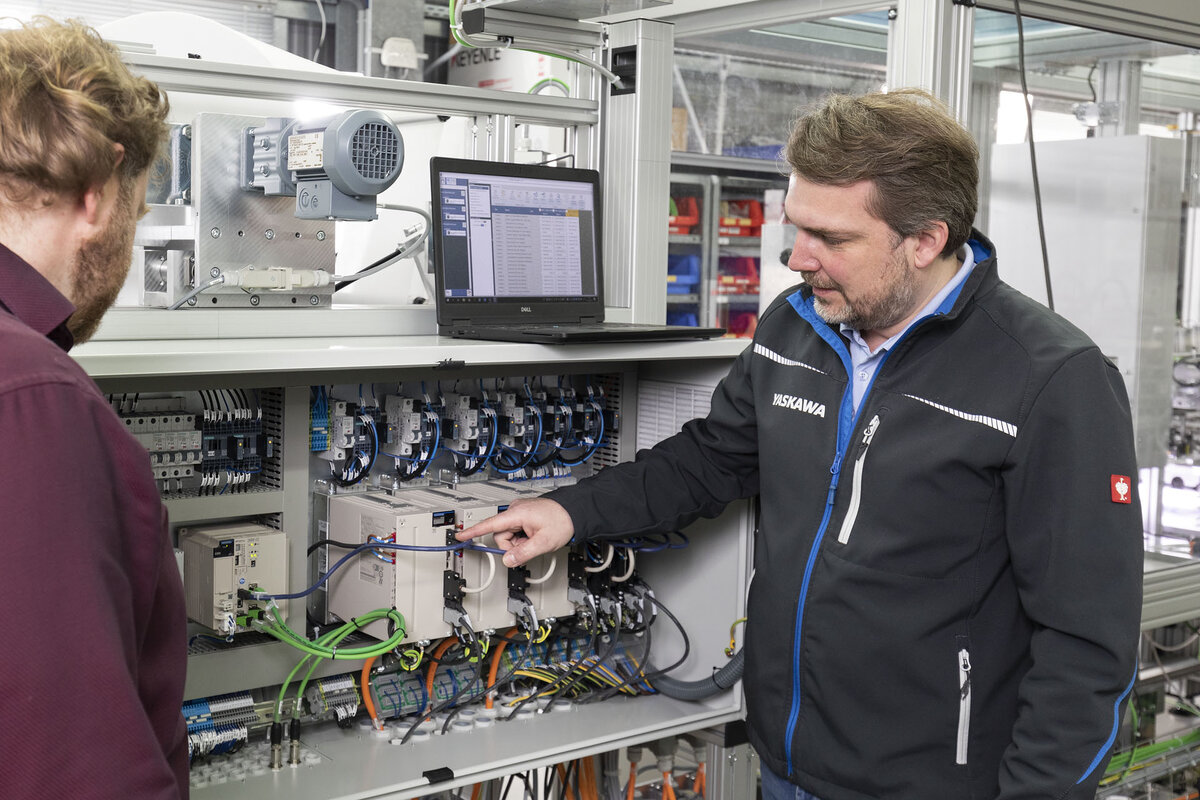
Automation technology for a smooth production process
As in most of their systems, the Unimatic designers used a Siemens PLC to control the machine in the mask production system. When looking for the best solution for smooth-running mask production, the technicians quickly came across Yaskawa, whose MP3300iec machine controller and Sigma-7 servo drives have already proven effective in many similar applications and also impressed the mechanical engineers. The machine controller already has integrated function libraries for cam control, which can easily actuate the flying saw function. The servo series is synonymous with rapid start-up, high production output and maximum operational reliability, all of which were equally important to the designers of the mask production system. There was also a large range to choose from. The series now includes narrow single and double-axis amplifier modules for 200 V or 400 V. The responsive AC servo motors cover outputs from 50 W to 15 kW at supply voltages of 200 V and 400 V, boast extremely compact dimensions and are very quiet when running. They offer an impressively high resolution (integrated 24-bit absolute encoder), high dynamics as well as functions such as vibration suppression, suppression of machine resonance frequencies and a tuningless function for simple start up. By integrating these functions in the servo amplifiers, their performance is not limited by higher-level controllers or bus cycle times.
“However, it was not just the technology that impressed us,” adds Kahlau. “Working with Yaskawa was extremely enjoyable and everything went without a hitch. The expert assistance of the automation specialists with the drive design, the control concept and the connection to the PLC significantly accelerated our project, and whenever a challenge arose, it was dealt with very quickly. The service they provide clearly demonstrates quality and competence.”
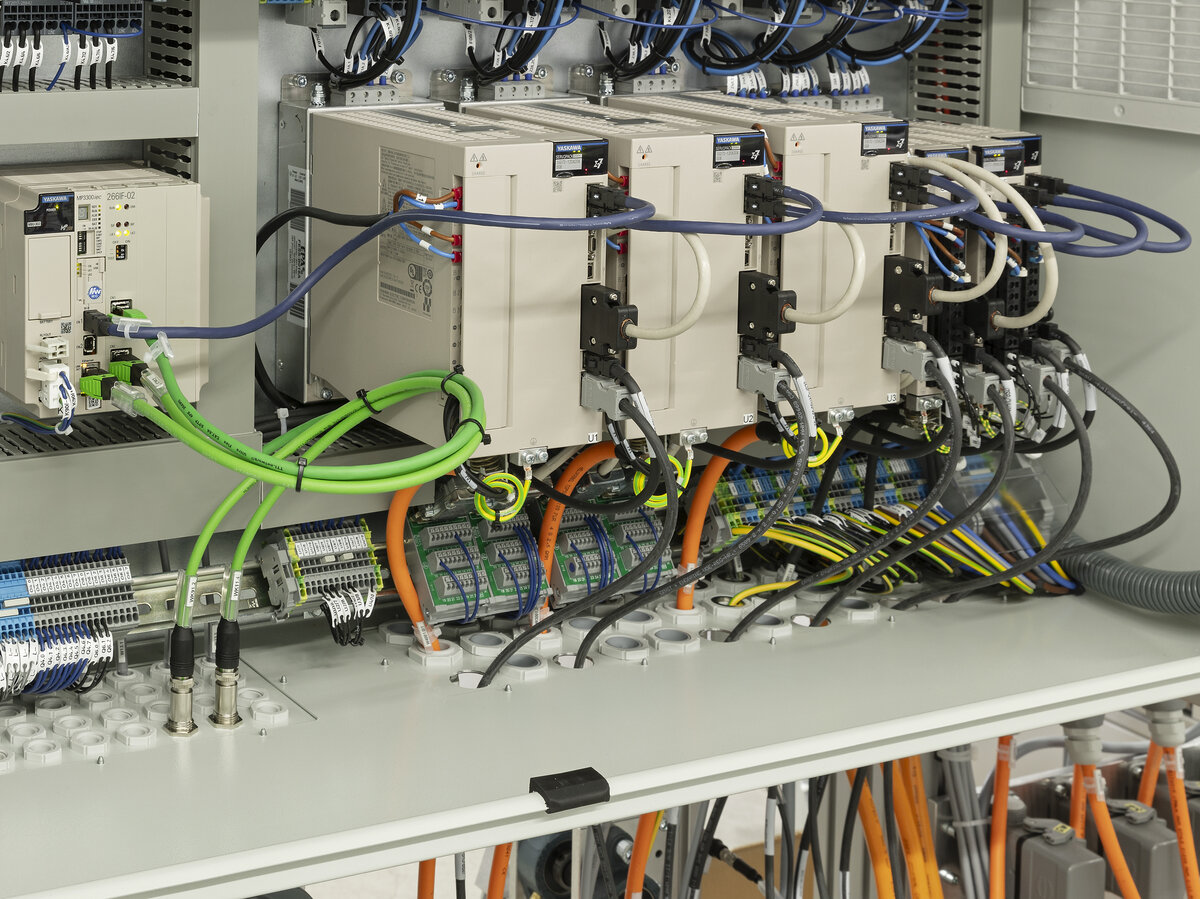
Six servo axes and a machine controller provide perfect synchronization
A total of six Sigma-7 servo axes (200 V) are used in each mask production system. The motor outputs are between 200 W and 1.5 kW. The largest drive is the one that drives the rollers for material transport. Two motors maintain the dynamic movement of the flying saws, in this case the ultrasonic tools that weld and shape the masks. Two further servo axes prepare the material for the wire hanger of the nose clip. The infeed area for the head straps and nose clips relies heavily on high positioning accuracy and extremely precise synchronization with the fleece.
The synchronization of the servo axes in the mask production system was easy to achieve thanks to the MP3300iec machine controller. The controller communicates with the servo axes via the MECHATROLINK-III real-time Ethernet bus, a high-performance interface designed especially for motion applications. With baud rates of up to 100 Mbps and cycle times of up to 125 µs, synchronization tasks that are significantly more complex than the mask production system can be undertaken. Programming is further facilitated by the MotionWorks IEC software tool with standard PLCopen and Yaskawa-specific function blocks (e.g. cams and electronic gears), which are available free of charge and which significantly simplify system programming. In addition to PLCopen function blocks, MotionWorks IEC also includes functions such as visualization tools, camera systems, conveyor tracking, and a group toolbox to support G-code. Together with the machine controller, the function blocks also allow the control of delta kinematics and multi-axis robots.
The Yaskawa machine controller is connected to the PLC of the mask production system via Profinet. However, the higher-level PLC is not burdened with the task of synchronization. The machine controller, which controls a number of areas including pneumatics and safety, acts as a master and specifies the sequence and the cycle of the drives. During ongoing production, the controller establishes the trigger points. For example, if there is a delay at a particular point in the system, the synchronization adapts to this delay to prevent a break in production. The solution has proven very successful. Eight mask production systems have now been delivered and put into operation.