Our industry-leading, high-speed industrial robots include high-payload, extended-reach, ultra-maneuverable seven-axis and unique 15-axis dual-arm robots.
Preventive maintenance management and retrofitting of industrial robots
Maximum availability – maximum security of investment
Industrial robots perform key tasks at different points of automated production. Stoppages for technical reasons can be reliably prevented – even when the manipulators and controllers have been in operation over many years, or even decades. The prerequisites for this are tailor-made maintenance strategies.
DIN 31051, also applicable to industrial robots, suggests various solutions and describes the main types of maintenance as corrective, preventive and predictive. Corrective maintenance replaces worn parts and repairs defective system components in the event of a breakdown. This kind of unplanned stoppage is extremely costly for companies. Experience also shows that selective corrective maintenance can result in accelerated wear of the machine.
Preventive maintenance management
According to DIN EN 13306, 7.1 the purpose of preventive maintenance management is to reduce the likelihood of downtime or restricted functionality. In systems with industrial robots the likelihood of failure is directly related to the lifecycle of the robot. This can be substantially improved by preventive maintenance management. From a long-term perspective, preventive maintenance management preserves the value of capital goods and provides input for long-term budgeting. An annual audit by the robot manufacturer documents the condition of the system and can serve as a basis for audits and maintenance planning.
Preventive maintenance management also yields tangible economic benefits. Assuming a 0.25% annual increase in efficiency and 4,000 operating hours per year, the downtime for a better maintained machine will be reduced by 10 hours. At an assumed hourly rate of 2,500 euros per machine, this amounts to annual savings of 25,000 euros.
In addition, long-term studies by customers have shown that a significant improvement in system availability results in substantially reduced inventory costs, as many critical replacement part components no longer need to be kept in stock. This also has a positive effect on risk assessment.
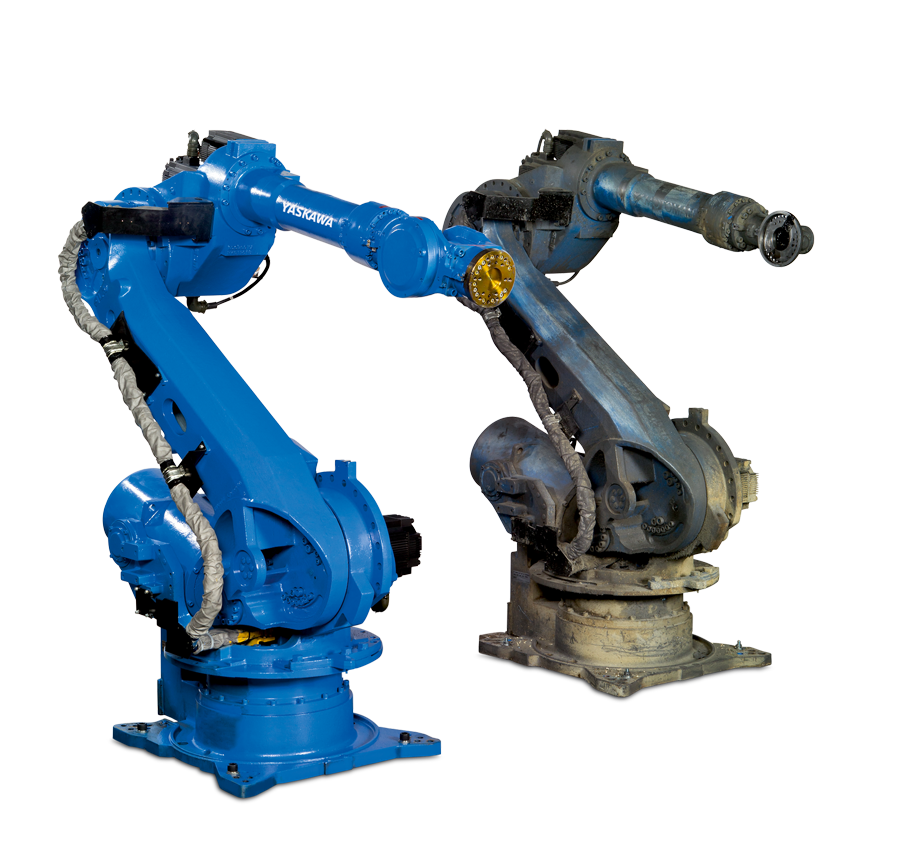
Retrofit
High availability and an extended lifecycle of industrial robots also mean a better return on investment. Whereas a product used to be designed for a total operating cycle of eight to maximum twelve years, today it is often 16 to 24. However, the actual lifecycle of a robot has remained unchanged at five to eight years, whereby retrofits or new acquisition during the product cycle should be considered.
As an alternative to cost-intensive new acquisitions, which often entail a generation change for the manufacturer and thus additional expense for reprogramming and personnel training, robot manufacturers also offer replacement units and systematic retrofit programmes in order to keep production stoppages to a minimum. The use of an identical model means no “major changes in machines” for the purposes of the Machinery Directive 2006/42/EC. No new safety inspection and no new CE label is necessary, which is why replacement and retrofitting programmes are often preferred.
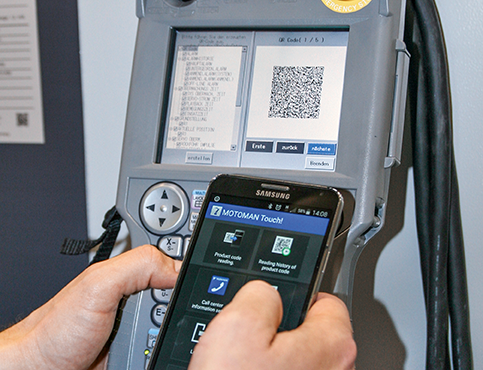
Software support
System-specific maintenance management can be created by predictive maintenance from the time of acquisition. The latter provides data that reflects the condition of the robot and system. Ongoing condition monitoring should reveal irregularities in wear at an early stage. On this basis it is possible to take suitable countermeasures or accurately schedule preventive maintenance.
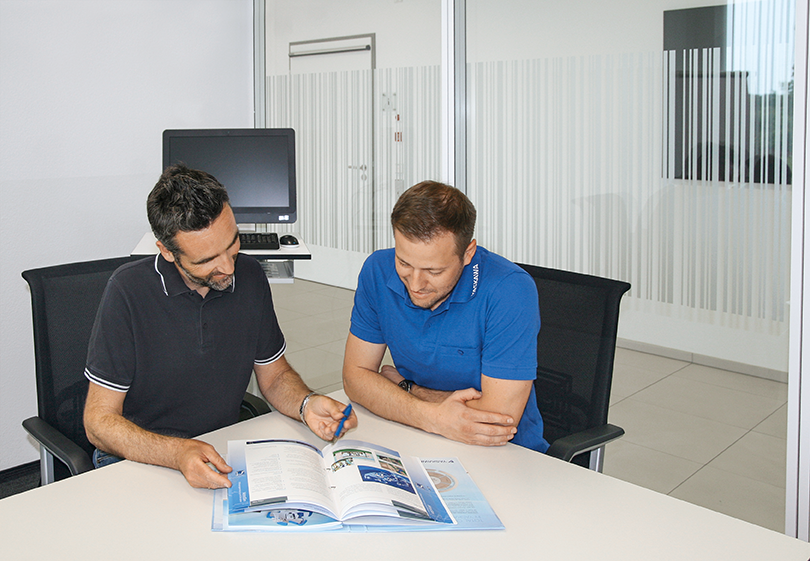
Total customer support
Nevertheless, regular maintenance also has its limits. The latter are often reached, for example, when the system with a robot is to be used for other purposes or converted to a completely new product. Again, it is expedient to re-use as many parts as possible. In contrast to a retrofit, a complete system overhaul usually means “major changes in machines” for the purposes of Machinery Directive 2006/42/EC. In this case, the safety technology must also be converted to the current state of the art, necessitating renewed CE-certification. Yaskawa covers this requirement with its engineering services and the CE and safety consulting portfolio.
Retrofit programs and security consulting are constituent parts of a broad service portfolio that Yaskawa has brought together under the heading “Total Customer Support (TCS)”. The focus is on preventive maintenance, service and spare parts support, as well as optimization, modernization and optimum all-round support over the entire product lifecycle. Telephone hotlines in all countries provide a central access point for technical problems and enquiries for all generations of Yaskawa devices. Training at the Yaskawa Academy rounds off its TCS: every year about 1,400 participants attend advanced training courses at the Eschborn and Allershausen locations.
Author: Siegfried Schauer, Supply Chain Management TCS, Yaskawa Europe GmbH – Robotics Division
Pictures:Yaskawa