Our industry-leading, high-speed industrial robots include high-payload, extended-reach, ultra-maneuverable seven-axis and unique 15-axis dual-arm robots.
Tooth for tooth: fast, reproducible and specification conformant
The deburring of gearing components is such a complex task that it has hitherto only been possible to automate it at an enormous cost, if at all. This has now changed with the robot-based RDC (robot deburring cell), a solution evolved by special engineering company Klaaßen Technologie GmbH from Rhineland-Palatinate. Besides sophisticated technical processes, the Yaskawa Motoman robots thus used offer speed, reproducible precision and simple operation while guaranteeing the highest standards. The first practical applications of the new RDC technology are already underway.
Whether spur, bevel or heavy planetary gears for wind turbines, with their complex geometries, gearwheels place exacting requirements in everyday production. That applies in particular to the deburring and chamfering of tooth and workpiece edges. For this reason, this process stage is difficult to automate – and only at great expense, e.g. with CNC machine tools.
Reversely, this means that in the majority of cases, gearing components are still being deburred by hand. This procedure is time-consuming as well as labour-and cost-intensive, not to speak of the physical demands at the workplace. But not only that: purely manual processing is a stochastic process, i.e. the results are always liable to a degree of variation. Workpiece edges cannot be exactly and reproducibly defined. Furthermore, the workpiece is never equally accessible to the operator from all sides.
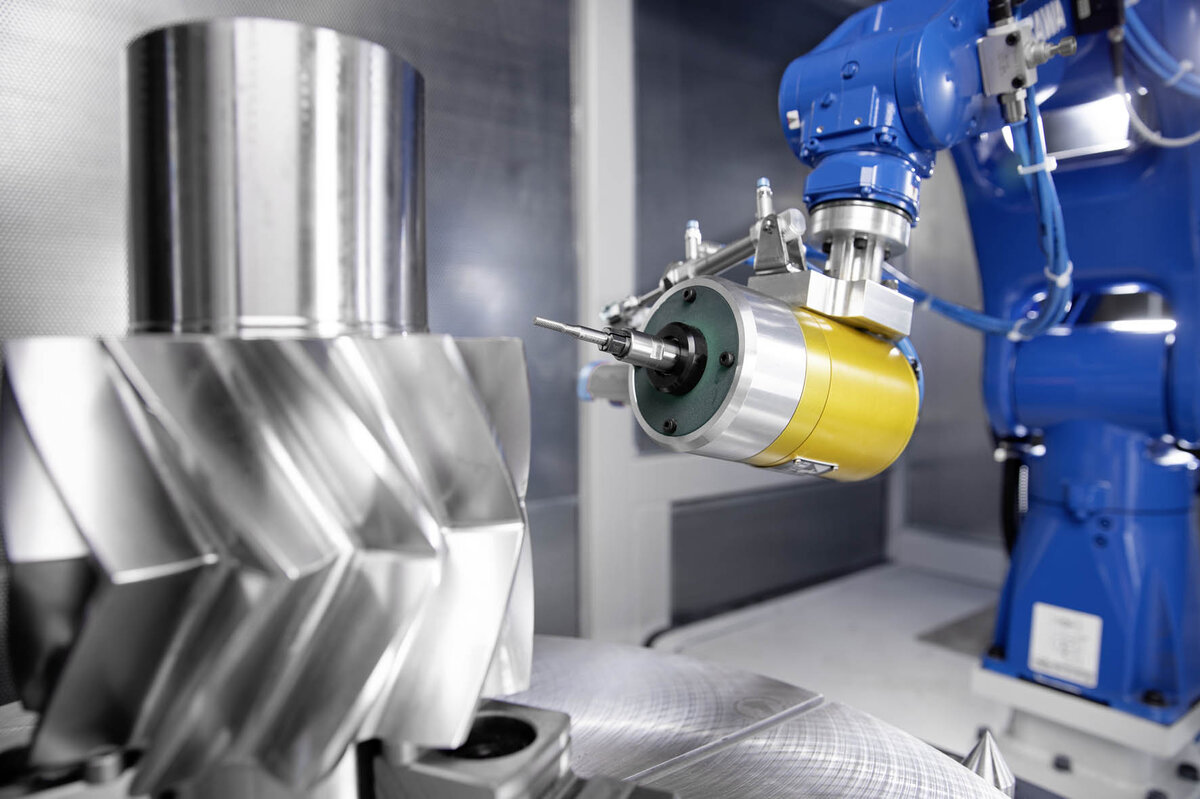
Robot-based alternative
Industrial robots offer a cost-effective and efficient alternative to deburring by hand or CNC machine. Following a three-year developmental period, Klaaßen Technologie GmbH 2020 presented a solution in the form of an RDC. The system combines intelligent software with a sophisticated tactile measurement procedure and efficient robot. Additional functions such as a twin-table concept or automatic tool changing round off the spectrum of applications.
As a consistently accurate (deterministic) process the RDC guarantees outstanding deburring quality with short cycle times and high productivity. At the same time, the cell offers broad diversification when it comes to workpiece sizes and forms: both fixed and individually programmable search patterns are available and possible for determining the respective deburring geometry, e.g. for spur gears, internal or palloid gears. A further feature of the RDC is that it is simple to operate and program, thanks to a simple variable control. Special CAM or teach-in processes are unnecessary, with the result that only minimal operational demands are placed on the employee in charge. The workers hitherto assigned to deburring can be easily familiarized with the new cell.
The intelligence of the cell sits in the graphically supported HMI controller, where it has access to the robot controller. The robot first of all measures the component, teaches itself independently and automatically starts the deburring or polishing process. It automatically searches for the relevant contour and decides on the curve on the tool. Or in the words of Thomas Damm, General Manager of Klaaßen Technologie: “The robot writes its own program.”
Robot as a central component
What sounds so simple is anything but trivial in terms of control and robot engineering. All these things taken into consideration, the decision-makers at Klaaßen Technologie opted for a Yaskawa Motoman robot. A major factor in this context was the Motoman YRC1000 robot controller, as Thomas Damm explains: “This versatile, high-performance controller type offered many possibilities in support of our concept – in particular a large number of variables that we have exploited almost to the full. The YRC1000 is designed to ensure a high level of path accuracy, coupled with fast and precise acceleration of the robot arm.” In addition, the controller is extremely compact and requires a minimum amount of space in the cell.
But Thomas Damm was also convinced by the hardware of the Motoman robot. Besides positioning accuracy and flexibility, he names a further reason: “Based on my many years of experience with robots, I can say with conviction that Motoman robots are among the most robust and mechanically reliable systems on the market – simply good Japanese engineering quality.”
The automation specialist speaks highly of the close partnership with the manufacturer: “Yaskawa afforded fantastic support in our development work for the RDC from beginning to end, and often beyond that.”
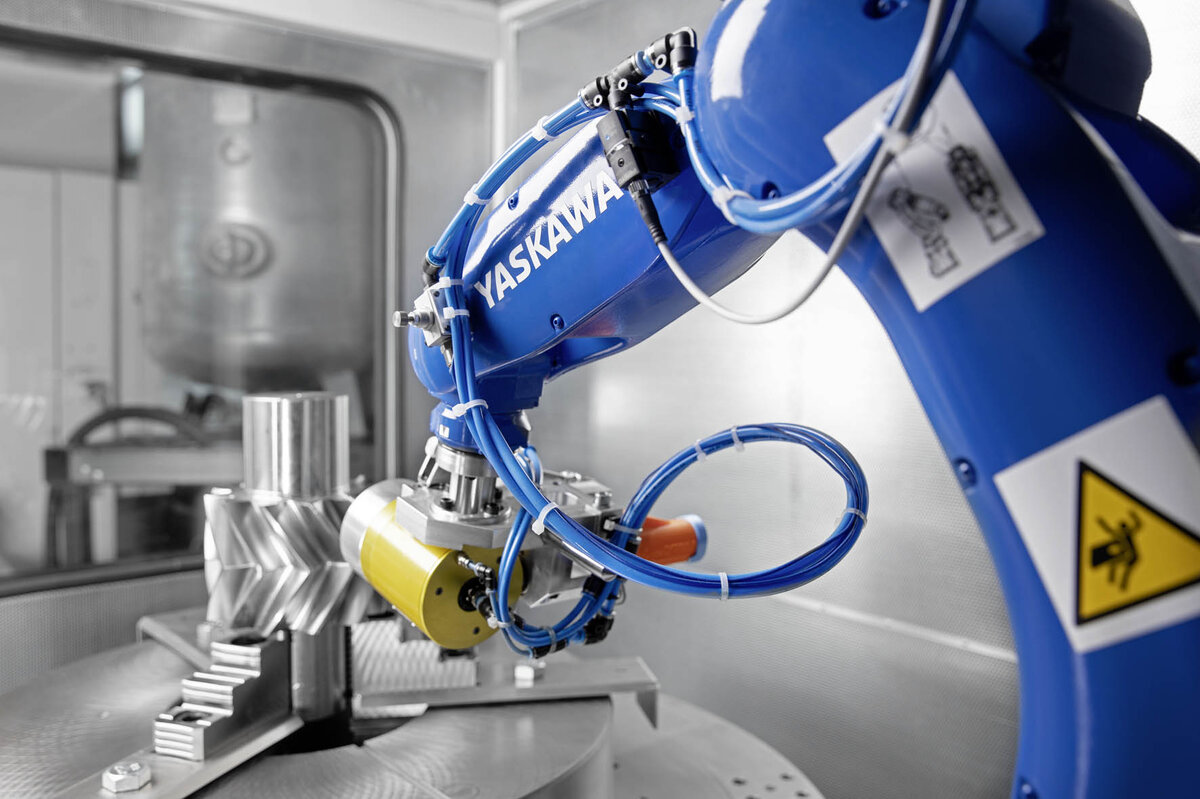
Solutions big and small
The diameter of the gears to be deburred naturally determines not only the cell dimensions, but also the robot specifications. Because of the significant potential of the RDC with large workpieces, the first practical applications were realized in this area. For example, an RDC 15 (designed for diameters up to 1.5 m) has already been successfully integrated into the production of a major contract manufacturer of wind power components.
With systems of this size, Klaaßen Technologie employs a Motoman MH50 handling robot with a payload of 50 kg. The six-axis robots of this series combine a high payload and high working accuracy on a small footprint – with a repeat accuracy of ≤ 0.2 mm and short cycle times. Thanks to a newly developed vibration control system, the axis speed and inherent rigidity of its gearbox can be used to achieve particularly fast acceleration with short movements.
But the RDC also offers interesting perspectives for smaller workpieces, as this current example shows: since 1967 F.J. Derichs Maschinenbau GmbH & Co. KG in Erkelenz has been manufacturing gears for all industrial sectors, from measuring pinions to heavy-duty drives. The traditional company is the first customer to adopt a further, smaller version of the RDC.
Here a compact Motoman GP8 with a payload of 8 kg has assumed the deburring operations. “This robot is easily the most accurate in its class and ideally suitable for filigree contours,” Thomas Damm justifies this decision. In addition, the robot is extremely fast and its design conforms to protective class IP67. The GP8 is so compact that the complete cell requires a surface area of only 2 x 1.4 metres. Its slim and curvaceous design enables the manipulator to reach deep into working zones, and the smooth outer surfaces facilitate cleaning. Only a robot cable is needed for the connection between the manipulator and controller. The advantages of this solution lie in less wear and a smaller footprint. Costs for maintenance and the stocking of spare parts are also kept at a minimum.
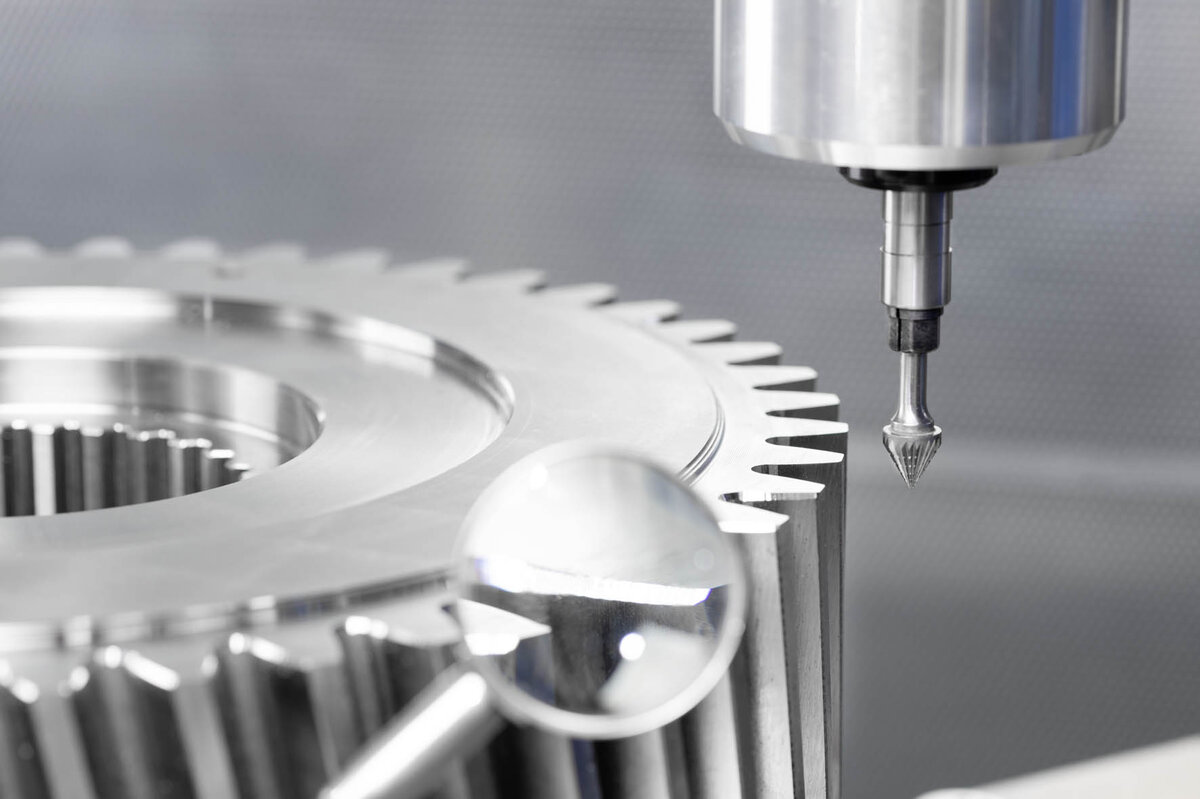
Conclusion and outlook
With the RDC, Klaaßen Technologie is setting new standards in the automatic deburring and bevelling of gearing components. Compared to manual work, time savings of up to 95 % can be achieved, while at the same time boosting productivity and quality. Deburring according to specs is likewise easily possible. Yaskawa Motoman robots have created the prerequisites for this convincing new development. Following the first successful practical projects, General Manager Thomas Damm already has his eye on the next innovation steps. A 3D sensor is proposed that will further extend the performance spectrum of the RDC.
Pictures: Yaskawa; Text: Frederic Oberle - Sales, YASKAWA Europe GmbH – Robotics Division, Allershausen
Contact for readers’ enquiries:
Tel. +49-8166-90-0
Fax +49-8166-90-103